If you want to understand why Parker stocks split, take a look here (see pointer) at the thin outline, a little less than 1/8 in. wide around the outer border of the stock face. That is where the majority of contact between receiver and wood occurs - that little tiny bit of surface area is what supports most of the force of recoil. There is also a section in the center, but it has been my observation that the factory stockers usually didn't get
as good wood-to-metal contact there because it isn't visible when the gun is assembled (I make this statement based on the observation that the thickness of the epoxy is usually a few thousandths greater in the center area than around the edges when a bedding job is examined). Consider that small area to distribute recoil force over, then concentrate it on the very outer edges of the stock which tends to create a spreading force, then remember that the rear of the top tang is shaped like a wedge and is being driven into the wrist under recoil, and it is a wonder that all of them don't split (and all of them don't). As good as the factory stockers were, it isn't humanly possible to get a 100% perfect wood-to-metal contact over the entire area where they meet. This means that recoil force is concentrated at pressure-points where wood and metal meet the tightest, and not over the other available surface area where the fit isn't as tight. Eventually the receiver will "set-back", or sink into the wood with repeated use as recoil crushes the wood fibers in the pressure-point areas. As the receiver sets back, the tang is driven into the wrist even further. The glass-bedding ensures that 100% of the surface area available for wood-to-metal contact is completely filled tightly. As a result, recoil force is evenly distributed over the widest possible surface area, and pressure points are eliminated. In addition, the epoxy is much harder than the wood, and receiver set-back is greatly reduced:[IMG]
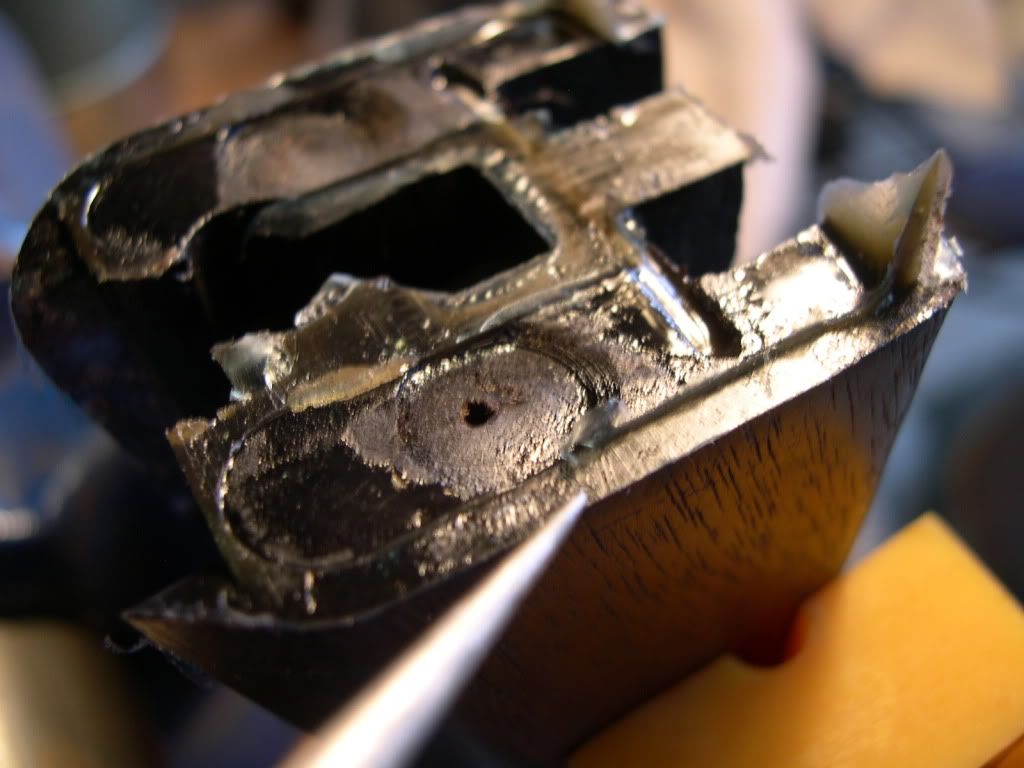
[/IMG]